Przyjrzyjmy się całemu procesowi od początku...
Proces stworzenia felgi aluminiowej to niezwykle fascynujący i emocjonujący czas, który obejmuje kilka etapów. Wszystko zaczyna się od wlewek ze stopu aluminium, do czego potrzebny jest masywny blok tego surowca. Aluminium jest podgrzewane do odpowiednio wysokiej temperatury, aby materiał stał się plastyczny, aż do jego stopienia, do czego służy specjalny piec z temperaturą ponad 800 stopni Celsjusza. Proces topienia aluminium jest kluczowy i stanowi podstawę do zapewnienia lekkiego i bardzo trwałego materiału oraz jego unikalnych właściwości. Co ważne, dokładny skład stopu felg DEZENT to jedna z najlepiej strzeżonych tajemnic w naszej firmie!
Po stopieniu aluminium jest ono wtłaczane do specjalnych form, a dokładniej do wlewnic, w celu stworzenia podstawowej struktury felgi. Na tym etapie niezwykle ważna jest kontrola określonej temperatury podczas procesu odlewania, aby właśnie uzyskać tą jednorodną strukturę.
Za każdą fazę produkcji odpowiada ktoś inny, w tym przypadku zajmują się tym asystenci produkcji ze stacji wytapiania i odlewni, którzy czuwają nad całym procesem topienia, transportu ciekłego aluminium do maszyn odlewniczych i jego ciągłego napełniania.
Czynnik ludzki jest niezbędny
Po etapie odlewania następuje pierwsza szczegółowa obróbka tzw. preformy w celu usunięcia nadmiaru materiału. Aby zapewnić absolutną precyzję, wykorzystuje się tutaj zaawansowane maszyny i technologie, ale także niezwykle istotną w tej fazie pracę ręczną. Powierzchnia jest wygładzana i sprawdzana pod kątem nierówności. Następnie konieczne są jeszcze trzy kroki. Zajmują się tym asystenci produkcji z działu odpowiedzialnego za prześwietlane promieniami Roentgen’a oraz obróbki mechanicznej i polerowania. Stała kontrola jakości jest jednym z najważniejszych i kluczowych elementów procesu tworzenia felgi za który odpowiada każdy poszczególny dział.
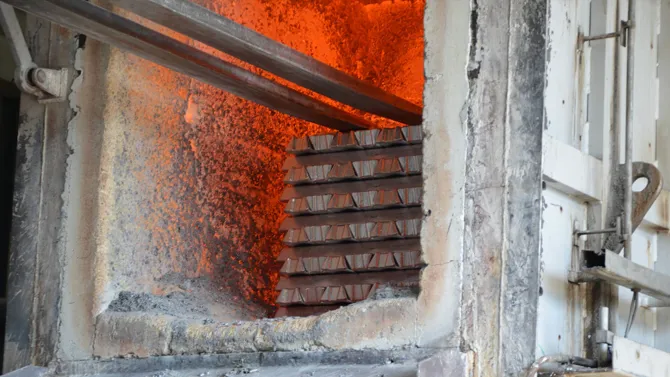
Jedenaście kroków do lakierowania
Po wstępnej wizycie w lakierni felgi aluminiowe podlegają czyszczeniu składającemu się z jedenastu etapów w specjalnej podczyszczalni, następnie przechodzą proces pasywacji oraz poddane są bardzo dokładnej metodzie powlekania proszkowego. Ze względu na zastosowanie właściwości elektrostatycznych, proszek bardzo dokładnie pokrywa powierzchnię obręczy docierając w każdy zakamarek, ale co ważne pokrywa ją równomiernie więc minimalizuje to ryzyko, że w którymś miejscu warstwa farby będzie zbyt gruba. Z kolei pasywacja powierzchni w technologii oznacza proces, który polega na celowym utworzeniu warstwy ochronnej na materiale metalicznym, zapobiegając w ten sposób korozji materiału podstawowego. Pasywacja aluminium tworzy na powierzchni konwersyjną powłokę chemiczną, która służy do zwiększenia odporności na korozję, taki stan osiąga się przez wytworzenie na powierzchni metalu cienkiej warstwy tlenków przy użyciu specjalnej mieszaniny środków chemicznych, które wpływają później na właściwości ochronne.
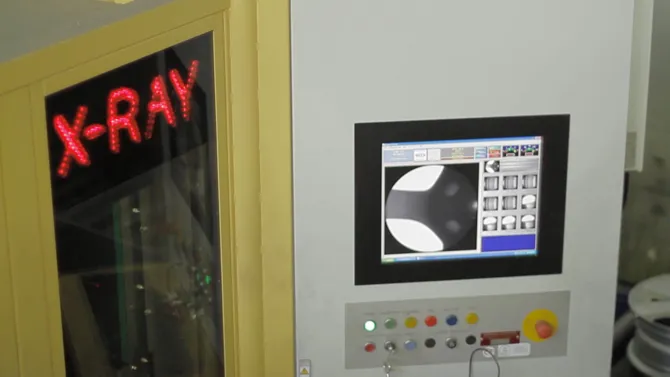
Po zakończeniu procesu czyszczenia felgi są one przygotowywane do właściwego procesu malowania, ale zanim to nastąpi są jeszcze raz dodatkowo oczyszczane z kurzu, pyłków i cząstek za pomocą wysokowydajnego specjalnego odkurzacza wykorzystywanego w technologii produkcji. W tak zwanym piecu malarskim pierwsza warstwa farby, czyli warstwa podkładowa, jest wtapiana w aluminiową felgę w postaci proszku. Ten proces barwienia stosuje się do materiałów, które nie są w stanie wchłonąć kolorów i farb. Powolne podgrzewanie obręczy powoduje, że właściwy nośnik koloru łączy się z warstwą podkładową, tworząc wyjątkowo silną ochronę. Dzięki przezroczystej powłoce zastosowanej na powierzchni obręczy, a więc trzeciej warstwie lakierniczej, tworzona jest pierwsza bariera przed czynnikami środowiskowymi, takimi jak niekorzystne działanie soli drogowej, błota, promieni UV i słońca oraz małymi zadrapaniami na jej powierzchni. Za proces ten odpowiadają asystenci z działu produkcji odpowiedzialnych za proszkowanie oraz pomocnicy produkcji, którzy pracują przy powłokach lakierniczych na mokro.
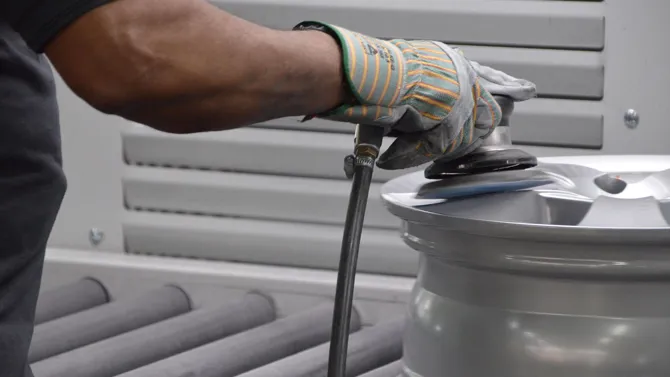
A co z tym TÜV?
Obliczenia komputerowe i symulacje mechaniczne to tylko jedna strona medalu – dzięki TÜV, która jest niezależną organizacją testującą, DEZENT przeprowadza również szeroko zakrojone i restrykcyjne testy jazdy. Tylko felgi spełniające rygorystyczne normy są zatwierdzane i przygotowywane do wysyłki. Wszystkie felgi od DEZENT posiadają certyfikaty TÜV, który mają na celu zagwarantowanie właścicielowi tychże produktów najwyższą jakość oraz bezpieczeństwo użytkowania na lata.
Dzięki sokolemu i niezwykle czujnemu spojrzeniu, ogromnemu doświadczeniu, kontroli i rutynie wykonywanych czynności, każdy egzemplarz felg DEZENT jest sprawdzany i przygotowywany do ostatniego etapu produkcji, czyli pakowania, a następnie wysyłki. Odpowiedzialni są za to asystenci produkcji na stanowiskach kontroli ostatecznej i pakowania. Dopiero gdy wszystko jest już porządnie zapakowane, felgi aluminiowe układane na palety i dalej transportowane do w pełni zautomatyzowanego magazynu wysokiego składowania, ale to już inna historia i na inny raz.
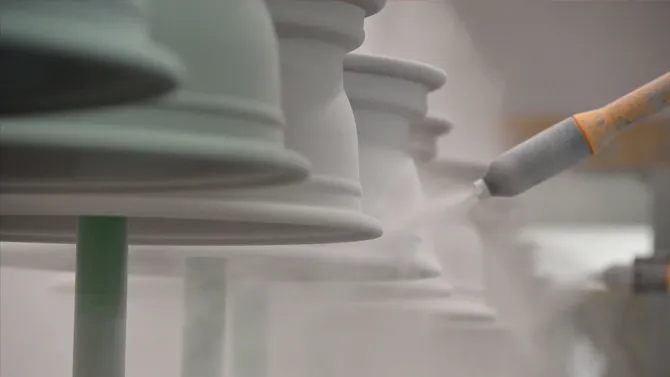
Tworzenie felgi aluminiowej jest zatem procesem wysoce złożonym technologicznie i bardzo precyzyjnym, wymagającym dokładnego i ostrożnego podejścia. Od fazy topienia aluminium po ostateczną kontrolę jakości, każda felga przechodzi przez wiele różnych etapów, aby spełnić najwyższe standardy i spełnić wymagania bezpieczeństwa, wydajności i estetyki. Chcemy podkreślić, że w procesie produkcji nic nie można pozostawić przypadkowi, ponieważ w przyszłości ma to wpływ na zwiększenie bezpieczeństwa kierowcy i pasażerów auta oraz daje gwarancję, że produkujemy felgi wyłącznie najwyższej jakości.
Jeżeli chcesz się przekonać, jak ten „cud technologii” wygląda na Twoim aucie, możesz szybko i łatwo sprawdzić to przy użyciu naszego KONIGURATORA 3D!
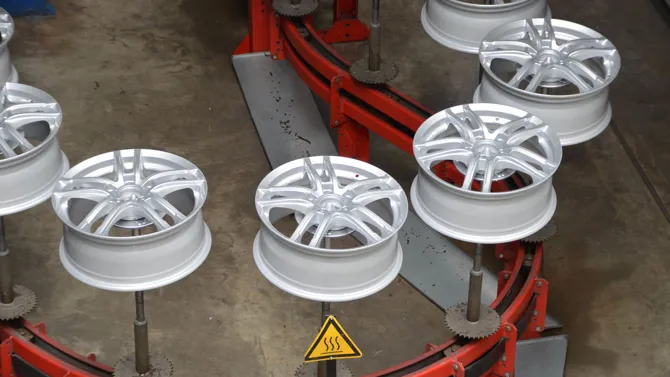